Without wood, we wouldn’t be here.
At every stage of societal evolution, wood has been essential to our progress. Fire, tools, shelter, traversing the seas, taking flight, even making music—wood has been instrumental in every one of these monumental leaps forward in human history. The symbiosis between wood and mankind is remarkable, even without factoring in the air we breathe.
With all the technological progress we’ve made and all the alternatives we’ve created, we have yet to find a way to improve on wood. It is still our most beautiful building material, and certainly the most adaptable and easiest to work with. Our finest furniture, our most stunning interiors, and even our most treasured musical instruments are still made of wood.
Being organic, wood is inherently unique, varying in character and color even within the same species, depending on the climate and the soil in which the trees grow.
Over the centuries, man has found ways to tame wood’s natural character, effectively domesticating this wild resource to yield a certain level of visual consistency, as well as high levels of performance predictability. In the end, though, you can take the wood out of the wild, but you can’t take the wild out of the wood.
And that’s exactly why we love it—but we must be careful not to love it too much.
nothing else is wood
If you’re specifying wood for interiors or furniture, “the wood look” probably tops your list of selection criteria. Nothing else has the richness, character, warmth, or depth of a wall made with finely finished cherry, or a conference table of clear mahogany.
There’s a reason that over 90 percent of all laminate designs imitate wood, as does much of the luxury vinyl flooring on the market, and even a growing volume of ceramic tile products: wood is part of our history and our heritage, the living soul of our natural and built environments.
The most practical and responsible way to use fine woods in your projects is to specify hardwood plywood decorative panels. Offering the best of both worlds, hardwood plywood is a value-engineered alternative to solid wood that provides maximum yield by using surface-quality logs as veneers on veneer-core and composite substrates that utilize wood fiber that would otherwise be landfilled or burned.
Hardwood plywood products on the market today offer a range of environmental certifications and LEED benefits, depending on where the trees were grown and how they were harvested, processed, and converted to furniture or value-added panels.
As you will see below, selecting the best hardwood plywood for your project requires not only an understanding of the materials themselves, but a high level of comfort with your sources of supply. PageBreak
stewardship, innovation, and resource utilization
In choosing your hardwood decorative panel supplier, you are in effect endorsing their treatment of the environment and their employees, as well as the vision of the role they play in the communities that host their production facilities and border their forestlands.
The Beauty of Wood: It’s all in how you cut it
Every log actually consists of two kinds of wood. “Heartwood” is the non-active or dormant center of a tree, usually distinguishable from the outer portion by its darker color; “sapwood” is the lighter-colored living wood occurring in the outer portion of a tree. The veneers from these two parts of a log may look very different.
As you can see in this PDF, the character of a woodgrain varies radically, depending on how the log is sliced into veneers.
Logging and lumber operations are part of North America’s industrial heritage, and are still the heart of rural communities in many states and provinces—or, were. Many lumber companies have gotten out of the business altogether, while others have sold out to corporate conglomerates, with predictable effects on the towns that once thrived around them.
These days, family-run companies that nurture their communities and maintain their own forests for the long-term health of the environment are few and far between. Luckily a few do remain, and they drive the industry with a deeper commitment to the future of their resources, the stability of their workforces, and true product innovation.
Three characteristics exemplify traditionally operated, family-run lumber companies:
- Ownership and nurturing of their forests
- Vertical integration of sawmill, lumber, and panel operations
- The ability to adapt quickly to fluctuations in resources and market demands
The idea of intelligent forest management is not new. It doesn’t take a rocket scientist to realize that if you don’t plant trees after you harvest them, you’ll soon run out of trees. But knowing up front that you can’t wait 100-200 years for your seedlings to mature to “old-growth” size before you need to harvest them will change your approach to resource management. Changes in construction methods and consumption trends play an important role as well.
As the post-WWII population and housing boom was ramping up, it became abundantly clear that our traditional reliance on solid wood for construction would soon decimate our forests. Smart mill owners quickly saw a mass market for a material that had been up until then a bit of a niche product: plywood.
Plywood panels were actually introduced nearly five decades earlier at the 1905 World’s Fair in Portland, Ore. This wondrous new material was strong, flexible, workable, and made use of lower-quality wood that would have otherwise been considered waste. It was far more resistant than solid wood to cracking, shrinkage, twisting, and warping, and less expensive to manufacture. Laid up with waterproof adhesives, plywood soon made its name in the military, found in everything from troop barracks to fighter planes.
The huge spike in the demand for housing after WWII drove plywood mills into high gear. They streamlined the production process and began to refine these multi-ply panels for higher and more specific application demands.
By the 1970s, most of the larger old-growth logs had been harvested and the economy was starting to stumble, causing a further shake-out of old-school lumber companies. More forward-thinking manufacturers began refitting their mills to handle smaller logs. They also diversified, particularly into particleboard and medium-density fiberboard (MDF)—composite panels made from the waste produced by sawmills and plywood plants that, again, would otherwise be landfilled or burned. The small amount of fiber left over was then used as biofuel to cogenerate power for production, reducing the need for fossil fuels and reducing landfill waste to nearly zero.
Engineers soon realized that these new composite panels could actually be incorporated into plywood panels for incredible stability, and that they represented an even more efficient use of wood fiber. PageBreak
core strength
Early plywood began as a problem-solving exercise, because solid wood has issues.
Even when kiln-dried to a stable moisture content, treated, and painted, wood naturally wants to move when subjected to temperature and moisture changes and as it ages. In an environment built of many different pieces and maybe many different species, wood will struggle against itself, leading to warping, splitting, and popping joints.
By slicing logs into veneers, turning them 90 degrees against each other, and gluing them into a panel, you offset the natural stresses of wood and create a much more stable product. Generally, thicker veneers of lower-grade (less perfect) wood are used in the center. For furniture and architectural panels, face-grade decorative veneers are peeled from high-quality logs, which means fewer trees have to be harvested to create many more square feet of furniture and millwork surfaces with real wood.
Before we get into the most recent developments in core technology, a brief explanation of “softwoods” and “hardwoods” is necessary.
- “Hardwood” is the general term used to designate lumber or veneer produced from trees that lose their leaves in cold weather, and produce seeds with a covering.
- “Softwood” is produced from trees that are usually needle-bearing or coniferous, which keep their “leaves” year-round, and produce seeds without a covering.
These terms do not indicate hardness in the physical sense: Balsa wood is very soft, but is considered a hardwood; bristlecone pine is quite hard, but is considered a softwood.
core options
In choosing the best core for different applications, the main criteria are:
- Weight
- Surface smoothness (compatible with your face veneer and finish choices)
- Screw-holding strength
Different types of cores all carrying the same face veneer may be specified for different applications in a project as needed. Here’s a look at some of the most common options. (All weights listed are approximate, and for ¾-inch thick, 4- by 8-foot sheets.)
While most traditional wood glues are made with formaldehyde, some hardwood plywood suppliers offer core materials made with no-added urea formaldehyde (NAUF) adhesive systems. Many also use only Forest Stewardship Council (FSC) certified wood, as well as ECC particleboard and MDF.
Most materials on the market are also California Air Resources Board (CARB) Phase 2 compliant, and some manufacturers produce panels that comply with CARB ATCM 93120 Ultra Low Emitting Formaldehyde (ULEF) Emission Limits, under Executive Order N-12-038.PageBreak
leed and other certifications
The LEED benefits of specifying hardwood plywood decorative panels depends largely on your core selection. The available LEED (2009) credits include:
- MR 4.1 and 4.2: Recycled Content
- EQ 4.4: Indoor Air Quality (NAUF)
- MR 5.1 and 5.2: Regional Materials
- MR 7.0: Certified Wood (FSC-certified)
Some specific LEED credits that may apply to particular products, depending on how they are specified, include:
- Particleboard core: All of the above with specific green material blends.
- CFC veneer core: EQ 4.4, MR 5.1, MR 5.2, MR 7.0.
- Veneer core: EQ 4.4, MR 5.1, MR 5.2, MR 7.0.
In addition to FSC, NAUF, and CARB 2, another relevant certification to consider when choosing a supplier is the ECC Sustainability Standard. ECC focuses on life-cycle inventory and other verifiable environmental practices, and highlights the responsible use of wood fiber and agrifiber by composite panel manufacturers. For more information, visit ECCproduct.org.
Here’s a summary of the green practices maintained by progressive, vertically integrated hardwood plywood producers:
- Company-owned forests are carefully managed and regenerated to ensure a constant supply of healthy wood fiber, as well as healthy, productive forestlands.
- Some forestlands are third-party certified, whether under the FSC, the Sustainable Forestry Initiative (SFI), or another program.
- Wood waste from one product line is utilized in another; i.e., off fall from the veneer plant is used in particleboard and MDF. Landfilling waste is kept to an absolute minimum.
- Fiber not suitable for any product line is used to fuel and heat the production plants, reducing fossil fuel dependence.
- Vertically integrated manufacturing facilities allow producers to utilize more wood under one roof, reducing transportation-related carbon emissions.
A combination of these factors has resulted in some composite wood panels being declared “better than carbon neutral” in a recent Life Cycle Inventory Analysis (LCIA).
advice from a veneer specialist
“Keep in mind, wood is a natural product,” says veteran veneer expert Bob Nurre. “That’s the beauty of it, and the curse.”
Wood’s Soulful Resonance
Wood is a living material, even after it has been harvested. When it comes to the world’s finest musical instruments—stringed instruments especially—scientists are still struggling to understand why wood’s resonance and tone continues to improve as the decades (or centuries!) pass, and as they are “played in.”
Before leaving the legendary Steinway factory in Queens, New York, each concert grand spends time in the “pounding room,” where a machine bangs on all 88 keys at once to open up its sound. Great mandolin players have been known to park new instruments in front of speakers blaring bluegrass recordings for hours on end to hasten the breaking in of the wood.
Instruments that have gone untouched for years, or even months, will start to sound dead, but they can easily be brought back to life simply by playing them. It’s almost as if the wood from which they’re made has a soul.
Photograph by Kenn Busch
“Trees have limbs on them, so you’re going to have knots,” he adds. “Every tree in the forest is different, and each sheet of veneer is a work of art unique unto itself. Each crate of veneer can also be quite different. Oak from Maine and Vermont isn’t the same as oak that comes from Wisconsin. And you can’t really specify that all your veneer comes from one place or another.”
Nurre, who has been in the business since 1980 and often works with architectural specifiers—sometimes helping them make selections in a room full of raw veneers—has seen the quality of available woods change over time.
“The old-growth logs are gone, and some species, like chestnut, have been wiped out by blight; you can’t get that at all anymore. So we’re working now with younger trees and some hybrids, and they are different in character than the woods we had 25 or 50 years ago. In some parts of the world it’s a different story. I worked for 5 years setting up a plywood mill in Russia, and saw virgin timber there that we haven’t had here for 75 years.”
When it comes to demand for face-grade veneer species, Nurre says even five years is a long time.
“The mix is always changing. Five years ago, oak was the most popular, followed by birch, with maple a distant third. Now, maple’s number one by a large margin. Alder, which was barely on the map five years ago, suddenly has a lot of interest; it started in the Northwest, and is making its way east. Red oak is now a distant third.”
Nurre notes that even though alder, which has a more rustic, knotty look, is popular right now, the straight-grain look hasn’t gone away. White maple, plain sliced for a straight grain, is similarly hot right now. “We did very little of that five years ago,” he says.
This article is advertiser sponsored
In some cases, designers try to use a less expensive veneer to try and mirror premium woods. Heartwood red birch, for instance, works well for this, but it’s hard to get enough veneer from the heartwood of a birch tree.
A word of advice if you’re planning to use a fair amount of wood in your projects: Be sure not to specify only from a small sample. Samples are very small parts of larger panels, so the piece you’re viewing probably won’t be representative of the character of a full sheet.
In short, nothing else looks, feels, or ages like wood. And while it is one of nature’s most perfect renewable resources, we must carefully manage our use to ensure future generations will have the opportunity to love it as much as we do. To that end, hardwood plywood decorative panels offer the best possible combination of natural beauty, engineered performance, and environmental responsibility.
References
- “Making the Most of Real Woods,” Interiors & Sources, November 2010
- Multiple publications, Roseburg Forest Products
- “The Hardwood Plywood Handbook,” published by the Hardwood Plywood and Veneer Association
- “What is the difference between a hardwood and a softwood?” How Stuff Works
About the Author
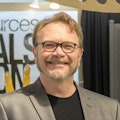
Kenn Busch
Contributing Editor
Kenn Busch is a longtime journalist, educator and public speaker dedicated to bridging the knowledge gap between materials, sustainability, and furniture and interior architecture. He is the founder of MateralIntelligence.com and ClimatePositiveNOW.org, two major resources for design and manufacturer specifiers.